
UNSHAPE REFRACTORIES
Ramming Mass
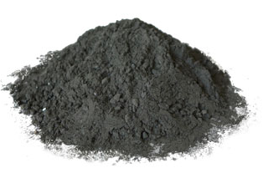
Is a powder shape material made from refractory raw material. Usually it has some proportion of binder
Ramming mass is a pre-blended Dry vibratables refractory made from a selected mix of SILICA GRAINS. This blend of grains along with a binder, BORIC ACID forms the working lining in an Induction furnace used for melting steel. The application process involves placing a cylindrical steel former within the furnace with equally spaced gaps on all sides. Then the ramming mass is filled into the gaps between the furnace wall and the steel former. This ramming mass is compacted with an electro vibrator. Once the lining is ready, steel scrap is charged, and the power is slowly turned up. Following a suitably designed heating cycle, the lining SINTERS (hardens) and then the steel scrap melts at approximately 1650 °C. Then the lining is ready to use, and scrap is molten and cast into billets or ingots. One lining may last for 5 to 50 cycles of melting, depending on the grade of steel cast, charge mix, melting time and the tapping temperature.
Is made into new type of inorganic binder material. There are four grades NT-1300, NT-1400,NT-1500,NT-1600.Refractory mortar is a specially engineered mixture of sand, calcium aluminate, cement, and fireclay. It is used to lay firebrick in places that are exposed to extremely high temperature. The refractory mortar is utilized only to build fire places and shall not be applied on hot faces. Refractory mortar is a mix of cement, sand, fireclay and, other specialized ingredients such as calcium aluminate. Fireclay is a set of various clays that can resist heat up to 3,000 degrees Fahrenheit. Just think of this as clay that has special heat resistant properties.
Refractory Mortar

Quicklime Refractory

Is calcined calcium carbonate or limestone. This used as source of CaO in the glass, enamel industries and refractories. This is often in combination with calcined and dolomite.Quicklime has a wide range of uses, including in the production of iron and steel, paper and pulp production, treatment of water and flue gases and in the mining industry. For the iron and steel industry, we also supply different fractions of both reactive shaft furnace-burnt and hard-burnt rotary kiln lime.
Gunning mixes are designed for refractories to be the instant adhesion to the surface and low rebond loss. The primary raw material use in gunning are low-iron sintered magnesia with more than 90% MgO and high CaO/SiO2.
Refractory Gunning Mixes or Refractory Gunning Masses are produced from granular refractory materials and applied by spraying on area with an air placement gun. It is mainly used for patching and maintenance applications for furnaces.
Gunning Material Mixes
